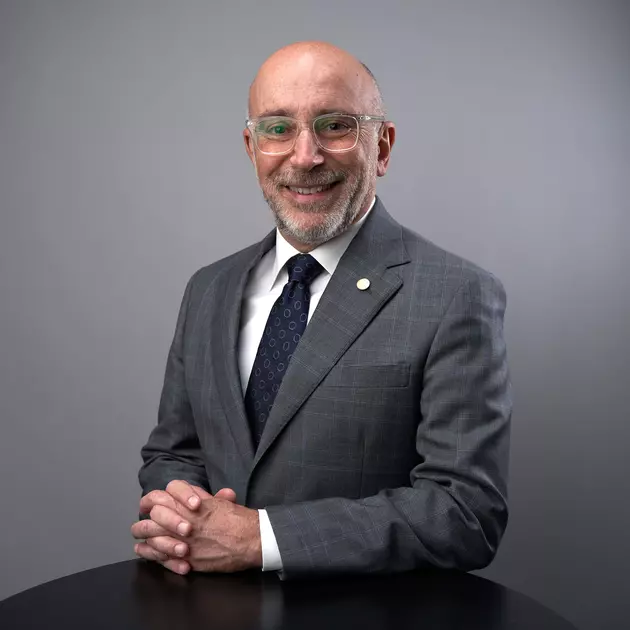
“Tenova HYL, the Tenova Direct Reduction Iron (DRI) competence center in Mexico, draws on its heritage of over 60 years of direct reduction technology development, since pioneering it back in 1957 with the world’s first industrial plant in Monterrey, Mexico. Over 40 DR modules have been supplied worldwide since then. From these solid foundations, we are building the future of the iron and steel industry offering the most sustainable solution for ironmaking available on the market, thanks to the use of hydrogen as reductant”.
Stefano Maggiolino
CEO Tenova HYL
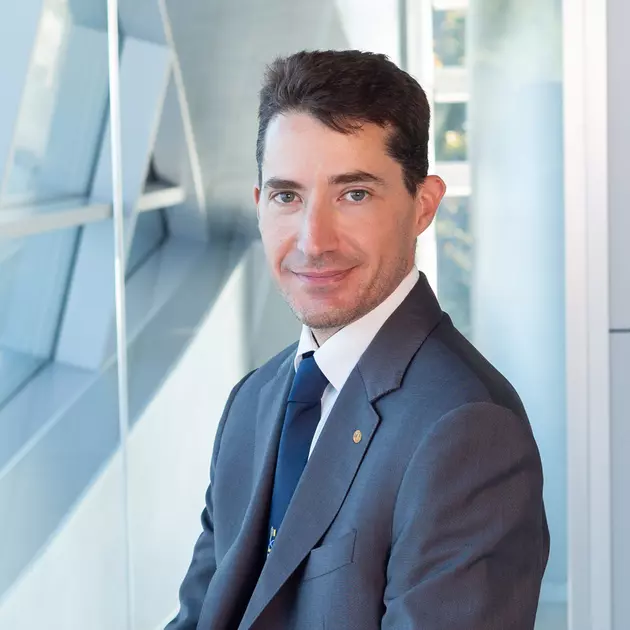
"The use of the ENERGIRON technology, jointly developed by Tenova and Danieli, is a definitive step towards a Green Steel era, with the possibility to use different amounts of hydrogen, up to 100%, as an alternative reducing agent in order to increasingly lower the carbon footprint without changing the standard and mature plant configuration."
Giacomo Mareschi Danieli
CEO Danieli Group